Carbon Brushes
Tailored brushes to the unique needs of your application, enhancing performance and longevity.
The sole purpose of a carbon brush is to conduct electrical current between the stationary and moving parts of the involved machinery. Usually made from carbon blocks, this essential component acts like a conduit. So, whenever these industrial brushes makes contact with the shaft in a generator or machine, it closes the circuit. The end result is – we get machinery that runs smoothly.
In case of Hatim Carbon, the quality of our carbon brushes reflects our expertise in engineering solutions for motors and managing voltage loads, a common issue affecting machinery lifespan. Our products are built to withstand prolonged use, whether in heavy-duty or intricate tasks. We believe in effective engineering through unified problem-solving, and our carbon holders exemplify this approach.
We don't compromise on quality. Ever.
Explore the power within: discover our diverse range of precision-engineered carbon brushes. From high-performance motors to industrial generators, find the perfect brush for your machine’s peak performance.
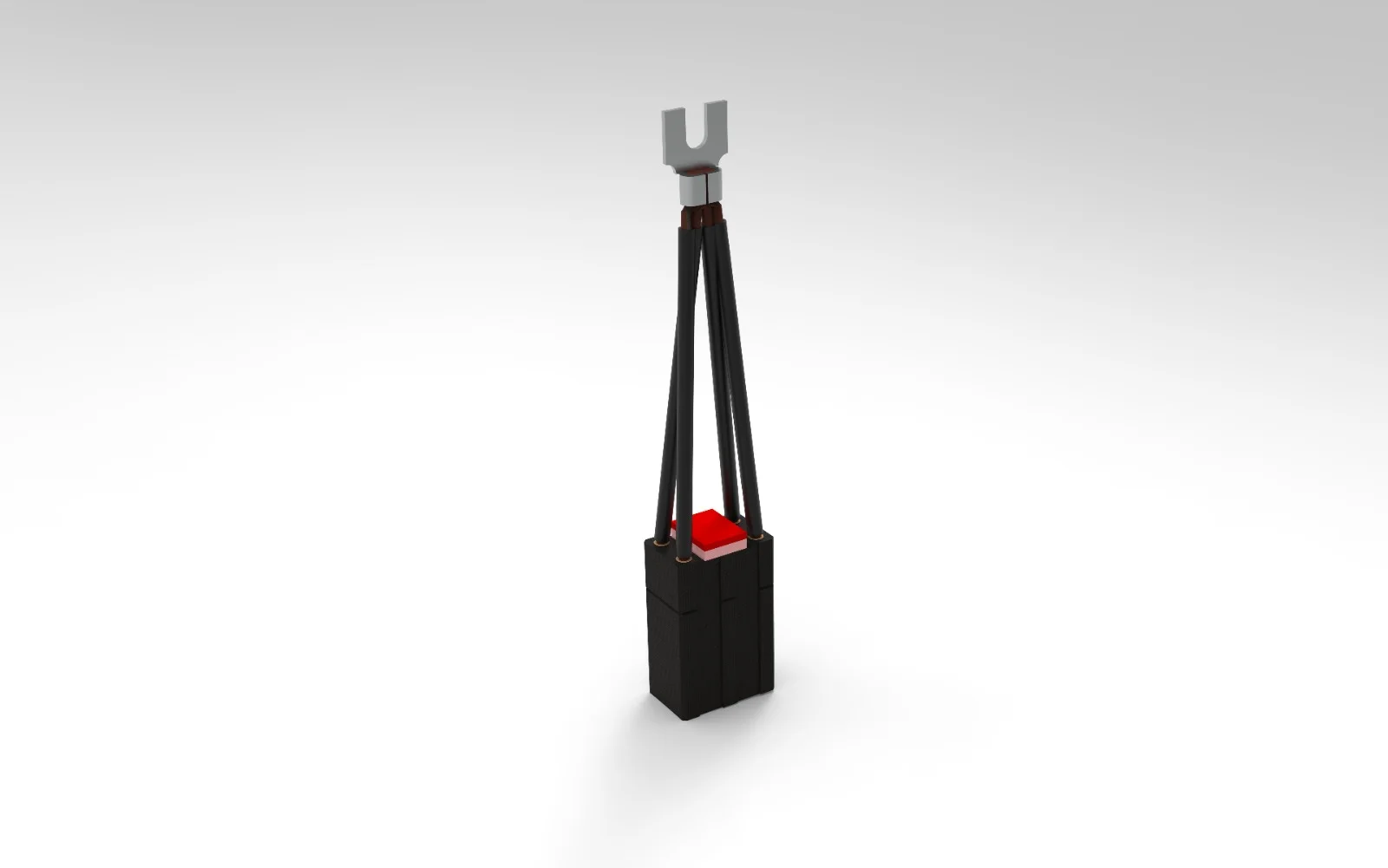
High-performance brushes with synthetic graphite for durability and reliable conductivity. Suitable for demanding industrial applications.
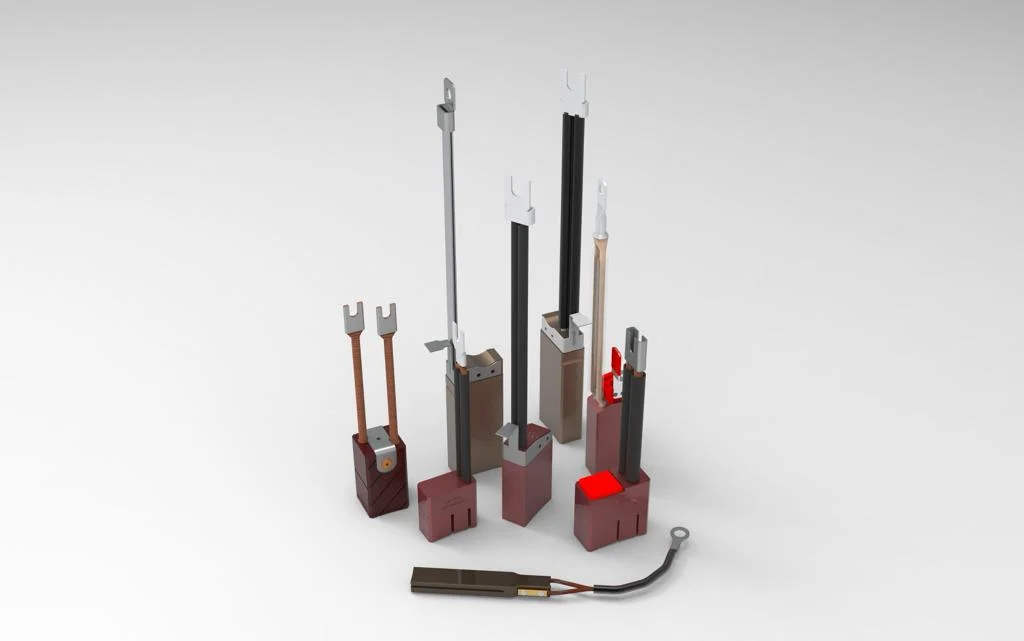
Blend of metal and graphite for high current density and consistent performance. Ideal for various motors and generators.
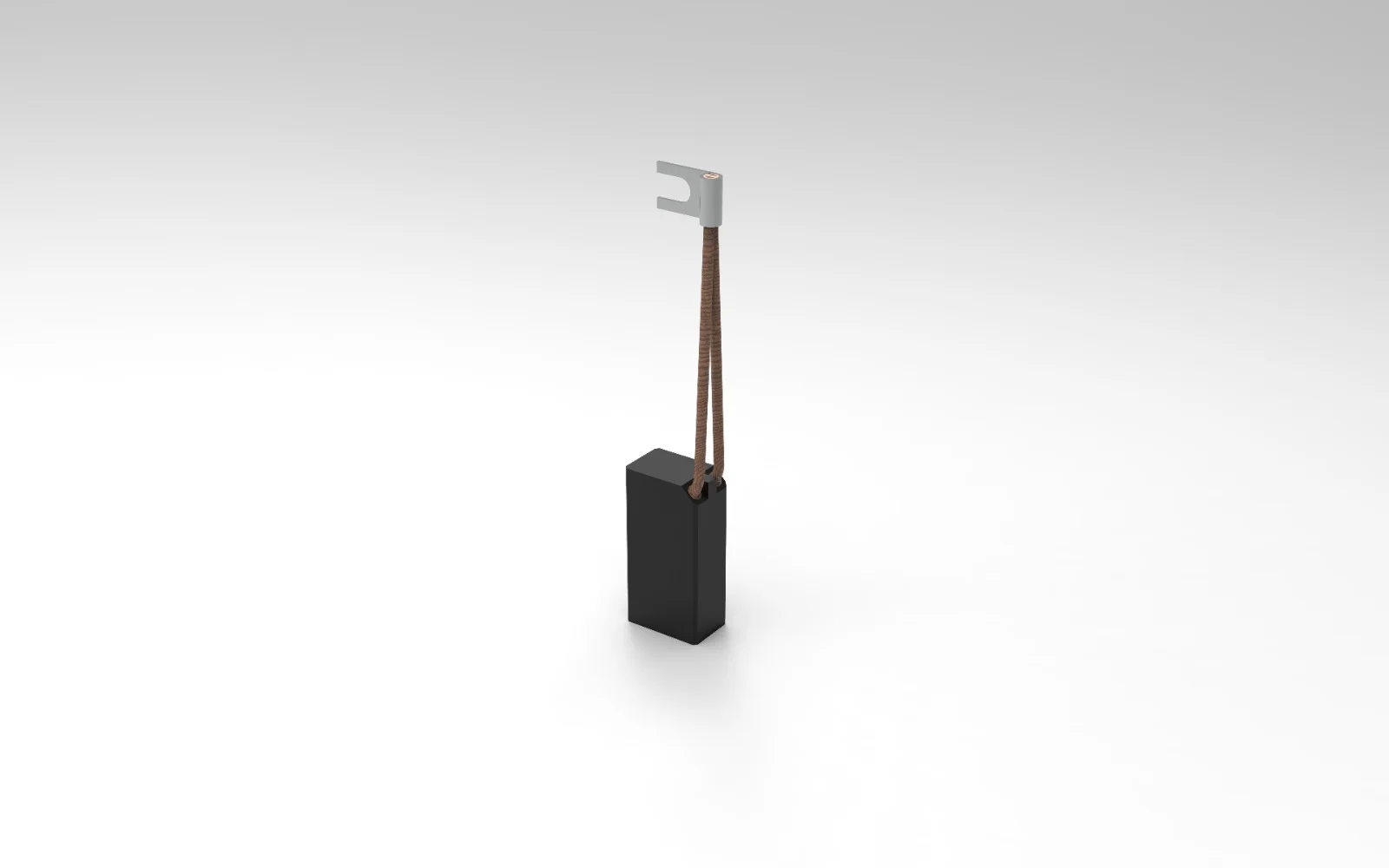
Versatile brushes with high-quality carbon for excellent conductivity and wear resistance. Commonly used in a wide range of electrical devices.
Upgrade Your Brush Gear Today
Get Expert Guidance on Choosing the Right Carbon Brush for Enhanced Performance & Lifespan.
Benefits of Using Carbon Brushes in Your Machinery
Overheating, responsible for 55% of motor insulating failures, stems from poor power quality or high temperatures. Every 10°C increase halves motor insulation life. Carbon brushes with high electrical resistance and mechanical strength, along with effective commutation and cleaning, can eliminate this risk.
When an electromotive force (EMF) is induced in a coil, it can lead to a surge of current. To avoid this, brushes are strategically placed to short-circuit the coil, preventing EMF buildup. This safeguards the involved motors against sparking in commutator segments.
Excessive voltage fluctuations strain motors. Carbon brushes minimize electrical noise from arcing between brushes and the commutator (DC) or slip rings (AC). This noise, if unchecked, disrupts electronic devices and equipment, inducing further voltage instability.
Carbon brushes boast a high melting point and exceptional wear resistance against commutators or slip rings, ensuring durability in demanding conditions. Their self-lubricating properties reduce friction, while stable electrical contact maintains consistent performance and while its inherent corrosion resistance prolongs motor lifespan.
Why Choose Carbon Brushes by Hatim Carbon
As a dedicated Carbon Brush Manufacturer, our mission has always been to set the standard as an ‘industry essential’ by delivering top-notch products.
We prioritize crafting Carbon Brushes that exceed industry standards in quality and lifespan. With years of experience, we’ve mastered our manufacturing process to ensure precision and a perfect fit for your machinery. Hatim Carbon stands shoulder to shoulder with other top Carbon Brush Suppliers in the industry. Our brushes are built to last, with remarkable shunt tolerance and crafted from premium raw materials, guaranteeing exceptional performance throughout their lifespan.
Get in touch with us to discover why teaming up with an Industrial brushes manufacturers like us can improve your machinery workflow, especially when dealing with issues like voltage fluctuations and overheating.
What sets us apart ?
Several process and production methods in our brushes give us an edge over our competition and allows us much more control on the performance of our brushes.
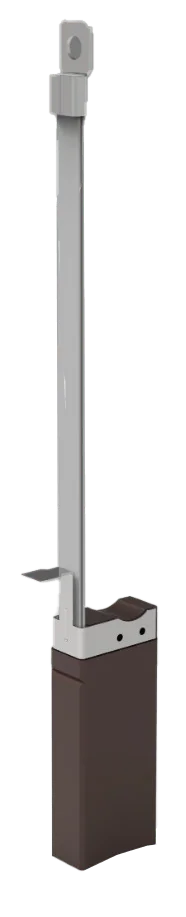